Indirect cable entries into “Ex” metal enclosures with “explosion-proof” (Ex “db”) types of protection with “increased safety” (Ex “eb”) junction boxes, with combined Ex “db eb IIC Gb” protections provide, among others, the benefits of increased “Ex” field service facilities for the assembly, inspection and maintenance activities of automation, telecommunication and electrical equipment and installations in classified areas containing flammable gases.
In all “explosion-proof” (Ex “d”) metal enclosures with internal sparking components or devices (which need to be protected by external enclosures because of the possibility of causing an explosion in an explosive atmosphere), the cables of the “external” power or control circuits must “enter” or “step into” the interior of the enclosures in order to be connected to the terminals of the respective devices. Examples of sparking devices or components that are installed inside Ex “d” enclosures are: circuit breakers, power switches, control switches, control buttons, contactors and relays.
There are basically two ways and techniques of manufacturing Ex equipment that users or owners of Ex equipment and installations can indicate in their typical Ex design details or specify in their documents or drawings for the purchasing processes, in order to allow these cable “entries” to be made the inside of Ex “d” metal enclosures:
- INDIRECT mode: NO need to open the lids of the Ex “d” metal enclosures
- DIRECT mode: WITH the need to open the lids of the Ex “d” metal enclosures
In cases of indirect cable entries, cables from external power, control or automation circuits are connected to terminal boxes of the “increased safety” type (Ex “e”), without needing to open the Ex “d” metal enclosures.
In cases of direct cable entrance, the cables of external power, control or automation circuits enter directly into the interior of the enclosures through Ex “d” cable glands (in cases of wiring systems through tray or conduit) or through Ex “d” sealing units (in cases of wiring systems through conduits). In these cases of direct entries, it is necessary to remove the covers to allow the fixation of the cable conductors to the terminals of the respective devices inside the enclosures and later replacing the respective covers (threaded covers or flanged covers fixed by means of screws).
In the illustration below are shown examples of installation of metal enclosures of the “explosion-proof” type (Ex “d”),containing sparking devices, such as circuit breakers, contactors, relays, or fuses, with cable entry in an INDIRECT and DIRECT mode.
Examples of setting up “explosion-proof” (Ex “d”) type metallic enclosures including sparking, with INDIRECT cable entry into the interior of the “explosion-proof” metallic enclosure by means of Ex “eb” terminal box external to the enclosure and DIRECT cable entry into the interior of the “explosion-proof” metallic enclosure by means of Ex “d” sealing units for conduits and by Ex “d” cable glands;
For eventual installation requirements of “explosion-proof” type metal enclosures which require the internal mounting of sparking components such as switches, contactors or circuit breakers with nominal current above 250 A / 25 kA, metallic explosion-proof enclosures with THREADED lids and with INDIRECT inputs must be used.
However, the utilization of equipment incorporating the concepts of combined protection by increased safety Ex “eb” with spark-gap devices (such as command switches, circuit breakers, control switches, power switches and contactors) individually certified as components with Ex “db” “explosion-proof” plastic enclosures (marking of the individual components Ex db eb IIC Gb U), may be considered as a suitable option with simplified requirements for installation, inspection and maintenance in hazardous areas compared to “traditional” metal “explosion-proof” type enclosures with flat gaskets fixed by bolts.
Example of “Ex” local control button installation showing internally sparkling components (electrical contacts) of the “explosion-proof” (Ex “db”) type, individually certified (Suffix “U”) in plastic enclosure and “increased safety” (Ex “eb”) terminals. Components with combined protection types Ex “db eb IIC Gb (U)“. Marking of the complete device: Ex db eb IIC T6 Gb IP 66 / Ex tb IIIC T80ºC Db IP 66
DIRECT cable entries into metal “explosion-proof” type enclosures (Ex. “d”)
Direct cable entries into Ex “d” metal enclosures by means of Ex “d” cable glands or by means of Ex “d” sealing units may show “deviations” or field installation difficulties, as for example improper installation of non “Ex” certified cable glands or Ex “e” certified cable glands made of plastic material or else sealing units which are not properly sealed or for which improper installations of non Ex “d” certified conduit fittings are made between the sealing units and the Ex “d” metal enclosures, as for example unmarked Ex “d” plugs and male/female couplings.
From a practical perspective, based on results of inspections carried out on equipment installed in classified areas it can be verified that a significant part of Ex “d” sealing units aren’t sealed at all, remaining totally empty, or are improperly sealed, without following the manufacturers’ recommendations. This type of “deviations” of sealing unit installations represent “ignition sources” in classified areas containing flammable gases, due to installation failures of Ex “d” fittings that are used for direct cable entries into “explosion-proof” type enclosures by means of conduits.
In the following illustration it’s shown an “example” of “Ex” equipment installation using direct power and control cable entry system to the interior of Ex “d” metallic enclosure, containing sparking devices.
Example of installation of “Ex” equipment with a system of direct cable entries of power and control circuits to the interior of a metallic enclosure of the “explosion-proof” type (Ex “d”) through the installation of a conduit sealing unit (found improperly totally empty), besides plugs without Ex “d” certification (on the right and left) and with the lack of installation of a sealing unit in the cable entry (on the left)
In this “example” it may be verified a sealing unit found improperly installed in classified area without any internal sealing, and it may also be verified the improper existence of a direct entry with the lack of installation of Ex “d” sealing unit. It may also be verified the existence of an Ex “d” sealing unit improperly installed in an incorrect position, with connection to the Ex “d” enclosure by means of a “stretch of conduit”, not meeting the requirement of “shortest possible distance” to the Ex “d” enclosure indicated in the Brazilian Technical Standard adopted ABNT NBR IEC 60079-14.
In the following illustrations are shown other “examples” of “Ex” equipment installations which have used the method of direct power and control cable entries into the interior of “Ex” enclosures, with the existence of undue “deviations” from “Ex” design, assembly and inspection services.
Example of Ex “d” instrument installation with direct cable entries into the enclosure by means of an Ex “d” cable gland improperly containing the installation of two cables in the same “Ex” cable gland
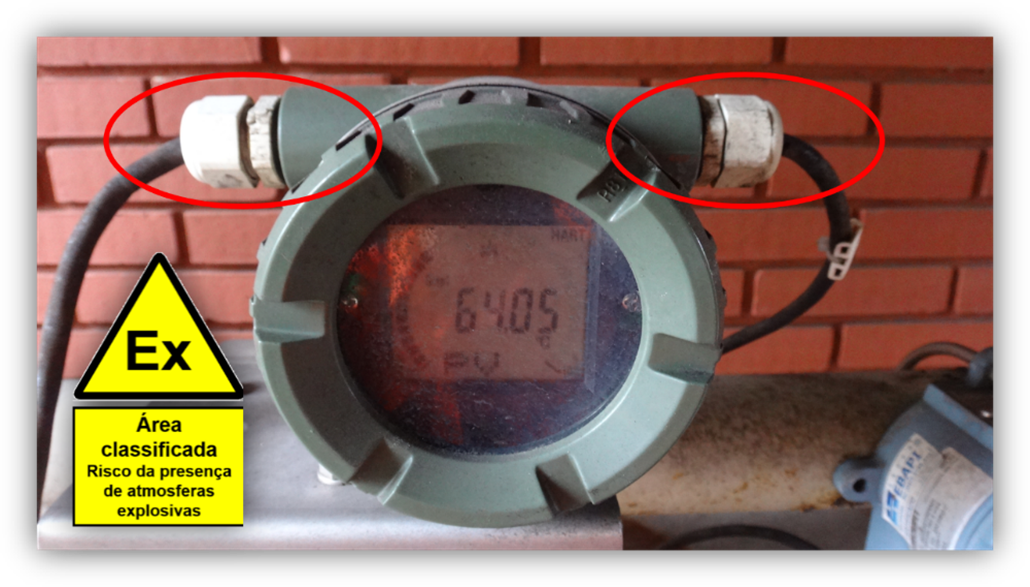
Example of Ex “d” motor installation with direct power cable entry system to the interior of an Ex “d” type terminal box through improperly installed flexible conduit without Ex “d” sealing unit
Example of Ex “d” instrument installation with direct cable entry system into a metallic “explosion-proof” (Ex “d”) enclosure by means of Ex “d” cable gland unduly containing the installation of two cables in the same “Ex” cable gland
Example of an instrument installation with a system of direct cable entries into a metallic “explosion-proof” (Ex “d”) enclosure by means of Ex “d” cable glands (incorrectly dimensioned, not tightening the cables)
Figure 26.7 – Example of instrument installation with direct cable entry system to the interior of the metallic “explosion-proof” (Ex “d”) enclosure by means of Ex “d” cable glands (unduly containing the installation of two cables). Source: Authors’ personal portfolio
Example of instrument installation with Ex “d” metal enclosure with direct cable entry system, with unused entry holes improperly sealed by plastic plugs, without “Ex” certification
Example of “Ex” terminal box installation with direct cable entry system into the interior of the enclosure by means of “Ex” cable glands containing improperly the installation of two or more cables in the same “Ex” cable gland
As can be observed in these “examples” of “Ex” equipment installation, the system of DIRECT cable entries inside metal enclosures with type of Ex “d” protection may present undue “deviations”, resulting from failures of “Ex” field services, related to failures of “Ex” design, assembly, inspection and maintenance services in classified areas.
In the next Part 2/3 of this Article on “Benefits of indirect cable entries in metallic equipment of the “explosion-proof” type” will be shown the characteristics of cable entries in Ex “d” metallic enclosures by means of external terminal box, with type of protection Ex “e” (increased safety), as well as the benefits obtained, from the points of view of assembly facilities inspection and “Ex” maintenance, and from the point of view of safety of the instrumentation, automation, telecommunications and electrical installations in classified areas, resulting from the use of the system of INDIRECT cable entries, in relation to the system of DIRECT cable entries to the interior of metallic housings of equipment with type of protection Ex “d” (“explosion proof”).
Roberval Bulgarelli
Technical Consultant on equipment and facilities in explosive atmospheres
Electrical Engineer, with Master’s degree in protection of power electrical systems (POLI/USP)
Book Organizer of the “The total life cycle of facilities in explosive atmospheres”